Black Box Shipping Automation
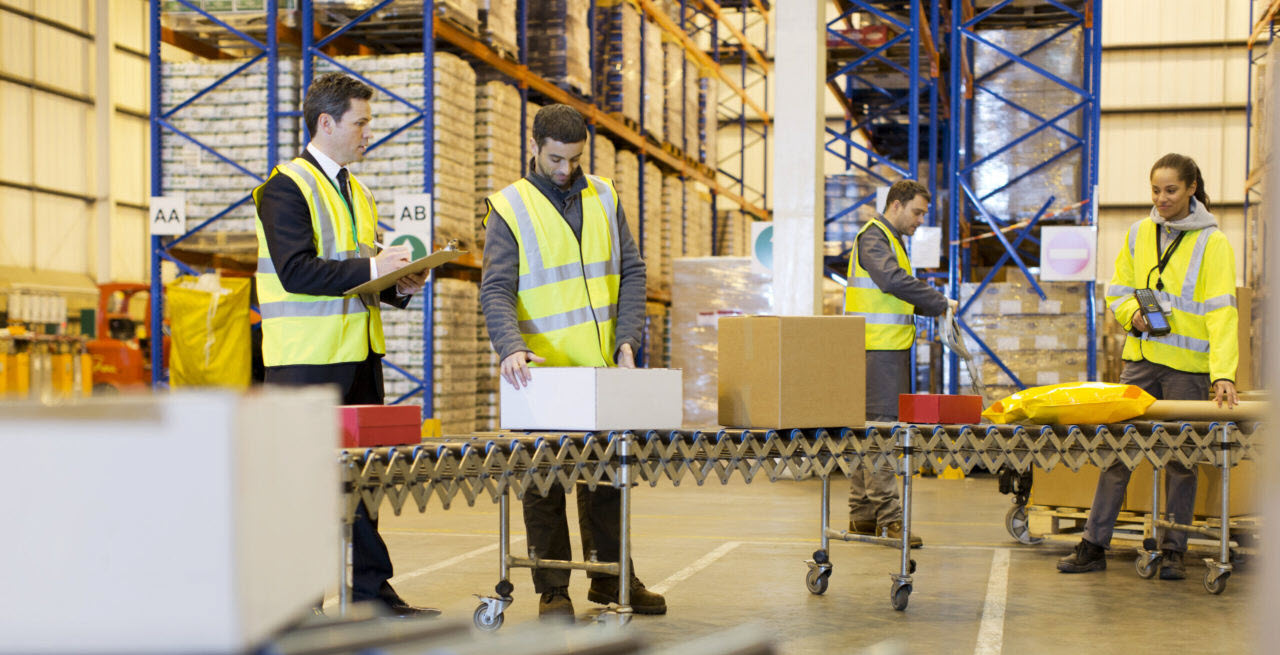
Definition
Blackbox Shipping Automation
Blackbox shipping automation is a systems integration workflow that automates many shipment processing decisions and tasks. It is accomplished by configuring two-way, real-time electronic communication between the host system (WMS, ERP, etc.) and the shipping system, eliminating the need for a shipping screen.
Reduce Shipment Processing Time and Tasks
Blackbox shipping automation makes it possible to eliminate many of the routine shipping tasks traditionally handled by warehouse workers, such as the keying or barcode scanning of an order number into a shipping screen to process the shipment.
Instead, the systems “talk” to each other and exchange decision data to actually process shipments behind the scenes, with no employee interaction necessary. Following is a simple example:
- The WMS or ERP host system starts by transmitting an electronic shipment “call” or processing request to the shipping system.
- The shipping software receives the order data, analyzes it, and automatically applies any business rules that are embedded into the software such as customer delivery preferences, carrier rates, and other criteria.
- The shipping software calculates the shipping cost, assigns a tracking number, and prints the shipping labels and other documents.
- Once complete, the shipping software electronically uploads the actual shipment details back to the host system.
Process More Shipments, Faster, with Lower Staffing Requirements
Blackbox shipping is a highly effective efficiency tool and cost-saver. By connecting your host system (WMS, ERP, etc.) to interface directly with the shipping system, you can reduce the touches required to fulfill orders, speed up shipment processing and eliminate shipping errors.
In many cases, because the systems are managing the tasks, you can reduce the number of shipping workstations that you’ve typically staffed down to one or a few stations that are available to handle orders requiring additional support.
The need to have separate packing and shipping workstations is also eliminated, as both tasks can be efficiently handled by a packer using a WMS screen at a combined pack/ship station.
The packer still physically packs the items and adds pack lists, product inserts, carrier shipping labels, other documents, but shipment rating, routing, and finalization are handled system to system, much in a fraction of the time required by staff on a shipping screen.
As a result, the time required to pack, confirm, and ship an order is reduced to a few seconds.
Free Up Staff for Other Warehouse Tasks, Reduce Seasonal Staffing
Many CLS clients have implemented Blackbox Shipping Automation to free up staff to focus on other areas of warehouse operations. Also, because shipping throughput is so much faster, they are often able to handle peak shipping volumes with existing staff.
Additional Blackbox Automation Applications
Blackbox interfaces can be configured to handle many areas in a warehouse including pre-label and release, shipment pre-manifesting, weigh-in-motion processes, scan/print and apply, and many others.
It can also be configured to provide actual shipping rates to your e-commerce customer’s shopping carts in real-time, while they are shopping.
Contact Us
Creative Logistics Solutions has implemented Blackbox Shipping Automation with our multi-carrier software for shipping, InfoShip®/Vx. CLS shipping systems are interfaced to a wide range of ERP and WMS systems. Please contact us for examples of our export shipping documents and a complimentary consultation.
Case Study: Dollar Shave Club Boosts Shipping Volume with InfoShip/Vx and Black Box Shipping Automation
Blog: Five Ways to Reduce Unexpected Carrier Back Charges
Blog: Four Proven Ways to Reduce Shipping Costs